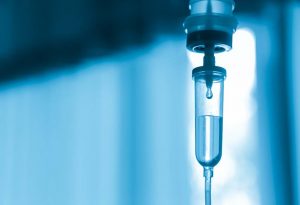
With the increasing demand for quality healthcare infrastructure and emergency medical services, the market for intravenous (IV) fluids has expanded rapidly across India and globally. Starting an IV Fluids Manufacturing business using BFS (Blow-Fill-Seal) technology is not only a profitable venture but also aligns with high standards of hygiene and automation. From hospitals to clinics and ambulances, IV fluids are a crucial part of modern medical treatment, making this business a long-term opportunity.
What is IV Fluids Manufacturing?
IV fluids manufacturing involves the production of sterile liquids packed in plastic containers, used to deliver nutrients, electrolytes, or medications directly into a patient’s bloodstream. These fluids are commonly administered during dehydration, surgery, trauma, and chronic disease treatment.
Modern manufacturing units use BFS (Blow-Fill-Seal) Technology, which is a highly automated process that forms the container, fills it with fluid, and seals it—all in one continuous operation. This minimizes human contact and ensures maximum sterility, a must in the pharmaceutical industry.
Applications of IV Fluids
IV fluids play a critical role in the healthcare and medical industry. Common applications include:
-
Hydration therapy for dehydration and fluid loss
-
Electrolyte replacement during surgery or trauma
-
Parenteral nutrition for patients who cannot eat
-
Drug dilution and delivery for antibiotics and anesthetics
-
Blood volume expansion in emergency care
The constant demand from hospitals, nursing homes, and healthcare centers makes this business highly sustainable.
Visit this Page for More Information: Start a Business in Intravenous Fluids Industry
Why Use BFS Technology in IV Fluid Manufacturing?
Blow-Fill-Seal technology revolutionized pharmaceutical packaging. Unlike traditional glass bottles or manually filled containers, BFS offers:
-
Aseptic processing with minimal human intervention
-
Single-use packaging ideal for sterility and disposal
-
Low contamination risk
-
High-speed and cost-effective production
-
Compact unit design with smaller footprints
Adopting BFS technology ensures compliance with international regulatory bodies like WHO, FDA, and GMP.
Read Similar Articles: PHARMACEUTICAL INDUSTRY
Types of IV Fluids You Can Manufacture
A well-planned IV Fluids Manufacturing unit can produce various types of fluids such as:
-
Normal Saline (0.9% Sodium Chloride Solution)
-
Dextrose Solutions (5%, 10%, 25%)
-
Ringer’s Lactate Solution
-
Dextrose-Saline Combination
-
Mannitol Injections
-
Sterile Water for Injection
-
Multivitamin and Electrolyte Fluids
Each product serves different clinical purposes and ensures a broad customer base.
Related Business Plan: IV Fluids, I.V. solutions
Raw Materials Required
Key raw materials for manufacturing IV fluids include:
-
Pharmaceutical-grade water (WFI – Water for Injection)
-
Sodium chloride, dextrose, potassium chloride, calcium chloride
-
Plastic granules (for BFS containers)
-
Sterile filters and cartridges
-
Labels, cartons, and secondary packaging
Quality sourcing and strict vendor controls are vital to ensure patient safety and compliance with drug regulations.
Related Feasibility Study Reports: I. V. Fluids
IV Fluids Manufacturing Process (Using BFS)
The IV Fluids Manufacturing process using Blow-Fill-Seal technology involves:
-
Water Purification – Raw water is purified using RO + UV + EDI systems and converted into WFI.
-
Solution Preparation – Precise quantities of solutes (like sodium chloride) are dissolved in WFI in a stainless-steel mixing tank.
-
Filtration – The solution is filtered to remove any microbial or particulate impurities.
-
BFS Operation – The plastic container is blow-molded, filled with fluid, and sealed—all in a sterile environment.
-
Leak Test & Inspection – Each unit is checked for leakage, particulate matter, and clarity.
-
Labeling and Packaging – The final product is labeled, packed, and stored in controlled conditions before distribution.
This process ensures high sterility and scalability for bulk orders.
Read our Books Here: Pharmaceutical, Drugs, Proteins Technology Handbooks
Equipment and Machinery Required
To set up a BFS-based IV Fluids manufacturing plant, the following machinery is essential:
-
BFS Machine (Blow-Fill-Seal Unit)
-
WFI Generation System
-
RO Water Treatment Plant
-
Mixing Vessels (SS316 grade)
-
Sterile Filtration Units
-
Online Leak Detection Machine
-
Visual Inspection Unit
-
Labeling and Packing Machines
-
HVAC and Clean Room Setup
A fully automated plant reduces labor requirements and enhances quality consistency.
Infrastructure and Layout
A medium-scale IV fluids plant will require around 10,000–20,000 sq. ft., divided into:
-
Raw material storage
-
Water treatment zone
-
Sterile manufacturing (Class 100 or Class 10,000 clean room)
-
BFS and packaging area
-
Quality control laboratory
-
Warehouse for finished goods
-
Office and utility space
Adherence to WHO-GMP, Schedule M, and ISO standards is mandatory for layout planning.
Regulatory Approvals and Compliance
The IV fluids business falls under the pharmaceutical sector, hence requires several licenses:
-
Drug Manufacturing License under the Drugs & Cosmetics Act
-
FSSAI license (if applicable)
-
GMP and WHO-GMP certification
-
Pollution Control Board NOC
-
Fire and Factory License
-
ISO 9001 and ISO 13485 (recommended for credibility)
-
CDSCO and FDA approval (for exports)
Proper documentation and audit readiness are essential to operate legally.
Cost of Setting Up IV Fluids Manufacturing Unit
The capital investment for setting up an IV fluids unit using BFS technology ranges from ?5 crores to ?15 crores, depending on:
-
Plant capacity (number of vials/bottles per day)
-
Degree of automation
-
Clean room setup and certifications
-
Location and utility costs
-
Regulatory compliance expenses
Working capital must also account for raw materials, utilities, staff salaries, and distribution.
Profitability and ROI
Despite high initial investment, IV Fluids Manufacturing promises strong returns:
-
Bulk demand from hospitals and healthcare distributors
-
High margin on sterile products (up to 30% per unit)
-
Scalability with export opportunities
-
Quick turnover and recurring orders
You can expect to reach break-even in 3 to 5 years, especially if you establish contracts with government or private hospitals.
Target Market and Sales Channels
Your customers include:
-
Government and private hospitals
-
Emergency medical services
-
Nursing homes and clinics
-
Medical distributors and wholesalers
-
Export agents and pharma chains
Distribution can be done through medical tenders, authorized dealers, or your own brand network.
Challenges and Risk Mitigation
Challenges:
-
High regulatory compliance
-
Initial cost burden
-
Technical know-how
-
Inventory wastage (if sterility is compromised)
Solutions:
-
Hire experienced pharma consultants
-
Outsource BFS machine operation to trained staff
-
Partner with raw material suppliers for timely sourcing
-
Establish robust QC systems and data logging
Risk management and quality assurance are the cornerstones of this business.
Future Scope and Market Trends
With increasing health infrastructure, pandemic preparedness, and demand for injectable therapies, the IV fluids sector is projected to grow at over 6–8% CAGR globally. India is becoming a hub for generic injectable manufacturing, making it an ideal time to enter this space.
You can also diversify into:
-
Antibiotic-filled IV fluids
-
Pediatric and veterinary IV solutions
-
Multivitamin or specialty IV nutrition blends
-
Contract manufacturing for global pharma giants
Final Thoughts
The IV Fluids Manufacturing business, especially with BFS technology, offers a high-growth, high-impact opportunity in the pharmaceutical sector. With its essential nature, robust demand, and export potential, this venture is ideal for entrepreneurs looking to build a sustainable and compliant healthcare manufacturing unit.
Click here to send your queries/Contact Us
Reasons for Buying NIIR Report:
- Our research report helps you get a detailed picture of the industry by providing an overview of the industry along with the market structure and classification.
- Our report provides market analysis covering major growth driving factors for the industry, the latest market trends and the regulatory framework of the industry.
- Our Report provides an analysis and in-depth financial comparison of major Players / Competitors.
- Our Report provides indispensable buyers’ data with their company financials as well as the contact details, which can be an important tool in identifying the target customers.
- Our report provides forecasts of key parameters which help to anticipate the industry performance.
- We use reliable sources of information and databases. And information from such sources is processed by us and included in the report.
See More Links:
- Start a Business in Asia
- Start a Business in Potential Countries for Doing Business
- Best Industry for Doing Business
- Business Ideas with Low, Medium & High Investment
- Looking for Most Demandable Business Ideas for Startups
- Startup Consulting Services
- Start a Business in Africa
- Start a Business in India